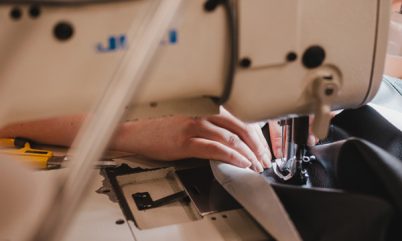
Having just returned back from a day trip to the NowyStyl factory in Jaslo city the main thing that stood out to me was not just the incredible size of the factories but also the overwhelming use of robotics and machinery.
The tour began in the armchair and chair production plant where we were immediately welcomed by the powder coating machinery. Every component to be coated is loaded onto a constantly moving conveyor and sprayed, first using robotics and then checked over and touched up by hand. The number of processes in the plant that were automated was staggering, I expected to see a lot of robots completing the simple or the mundane jobs but they were involved in almost every aspect of the process. A large percentage of welding was robotic, the outliers being mostly custom pieces which required a shift to manual production methods because of the different measurements and resulting lack of standardised jigs.
The foam production section of this plant was really interesting, all the foam used in NowyStyl is shaped in the same place their metal components are made, this not only cuts their transport costs and increases the efficiency of their assembly, but also allows them to use metal inlays in their foam pieces. Foam parts were either shaped from massive blocks or made using a mix of chemicals and a mould. When a metal inlay was added to a piece it would be moulded, this process was incredibly interesting to see, once again very little manual involvement aside from setting up the process and spraying the foam with a mixture that prevents bubbles and reduces resulting imperfections in the final piece. We were informed that foam offcuts are sent to an exterior company to be recycled into new blocks which were then sent back to the factory and used in production.
Moving to the upholstery factory there was a noticeable shift in the ratio of people to machinery, upholstery was a much more manual section of the production process. This is not to mean that the speed of production was in any way reduced, the upholsters worked with quick and practiced movements, completing both the seat and back of a chair in less than a minute. The increase in hands on work continued as we moved to the sewing area, where you could observe repeating rows of people working at sewing machines.
However, robotics were still interwoven with this section of the factory, leather and artificial leather sheets were marked by hand to show areas that possessed imperfections. They were then loaded into a machine that scanned the piece and calculated the most material efficient way to cut out the necessary patterns and proceeded to make said cuts. This was done with both single sheets of material and layered material, using a vacuum to ensure the sheets did not shift during cutting.
In the office furniture factory the balance between man and robot shifted once again, there were automated processes everywhere with just the occasional person working with the machinery. The first time you saw a person have contact with a piece of the product was half way through the factory when they were needed for unloading, quality control and sorting. The factory itself was vast, measuring 200 meters by 200 meters.
This trip has really brought to light the reliance of robotics within office furniture manufacture, looking at a room where there are robots as far as you can see and only a handful of people really put that fact into perspective.